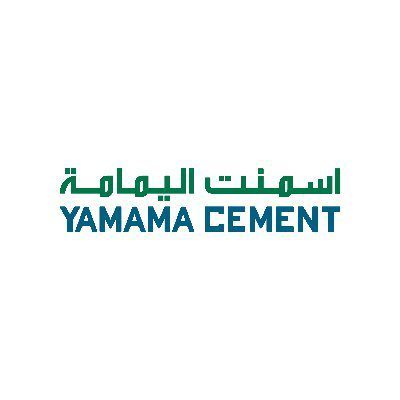
Yamama Cement modernizes and scales predictive maintenance with AI & IoT
Yamama Cement is a Middle East construction industry leader with a 40-year legacy. The stringent quality controls ensure exceptional products, and global reach spans international projects. Yamama cement uses a mix of reactive, planned and predictive maintenance.
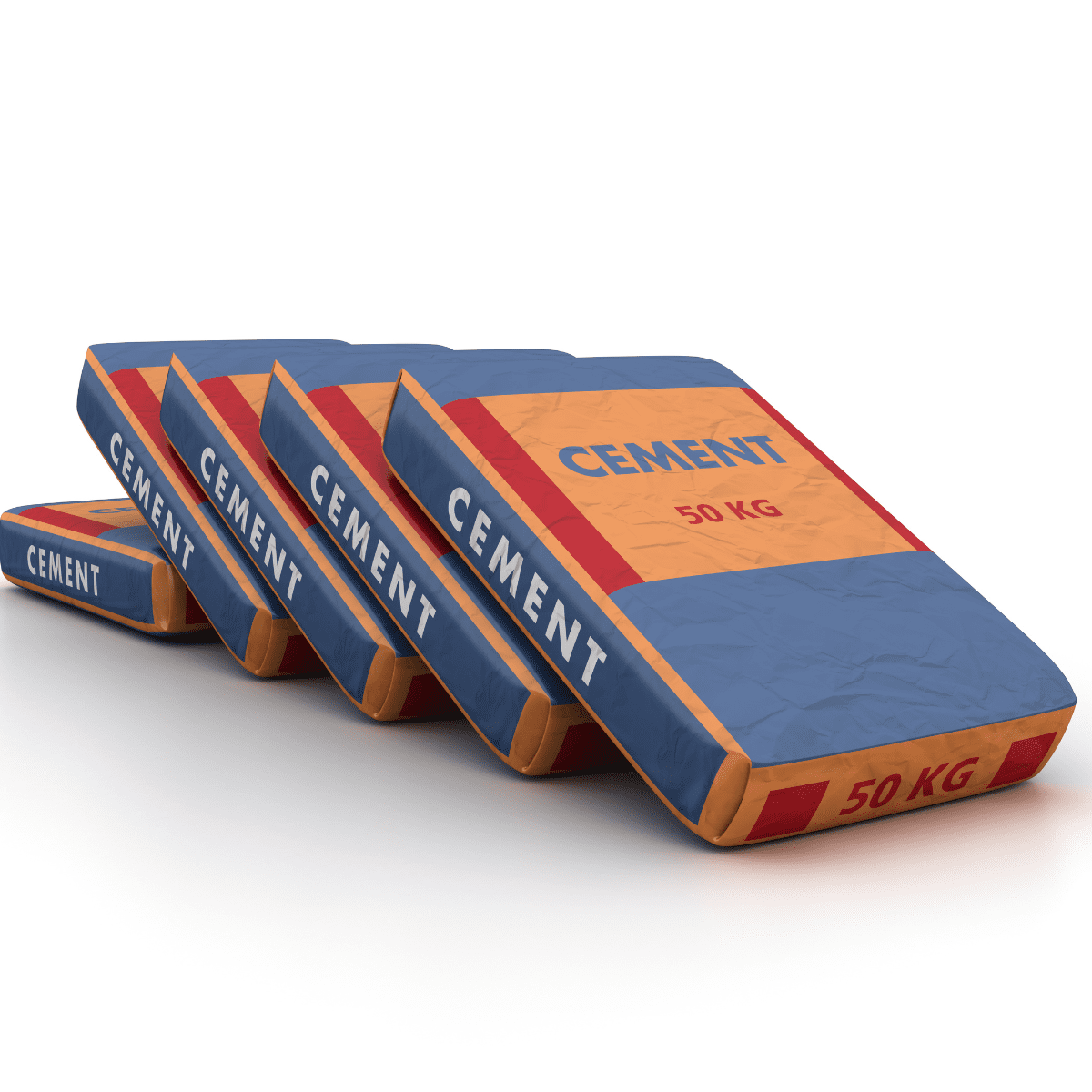
INDUSTRY
Cement
COMPANY SIZE
$ 270 Mn
YEAR FOUNDED
1956
KEY USE CASES
Improve asset reliability by leveraging IoT and Artificial Intelligence (AI) for real time condition monitoring and fault prediction. Reduce the vibration analyst time spend on data collection and analyzing data.
PRODUCTS & INTEGRATIONS
ioEYE Predict Sensors
ioEYE Predict Predictive maintenance AI Cloud
Azure AD directory.
15 days
Fast Implementation due to wireless sensors and SaaS
48%
More assets under digital predictive maintenance
3x
Improvement in accuracy and timely prediction of faults.
15 %
reduction in unplanned downtime
Reduced inspection possible for machineries installed in difficult to reach locations.
Increased asset life due to reduced ware leading to capex savings
Production loss prevented due to reduced unplanned downtimes
Reduced overall maintenance cost Reduced inspection possible for machineries installed in difficult to reach locations.
Energy Savings– As assets with faulty bearing, gearbox, poor lubrication and unbalance lead to more energy consumption. Timely intervention reduces energy use.
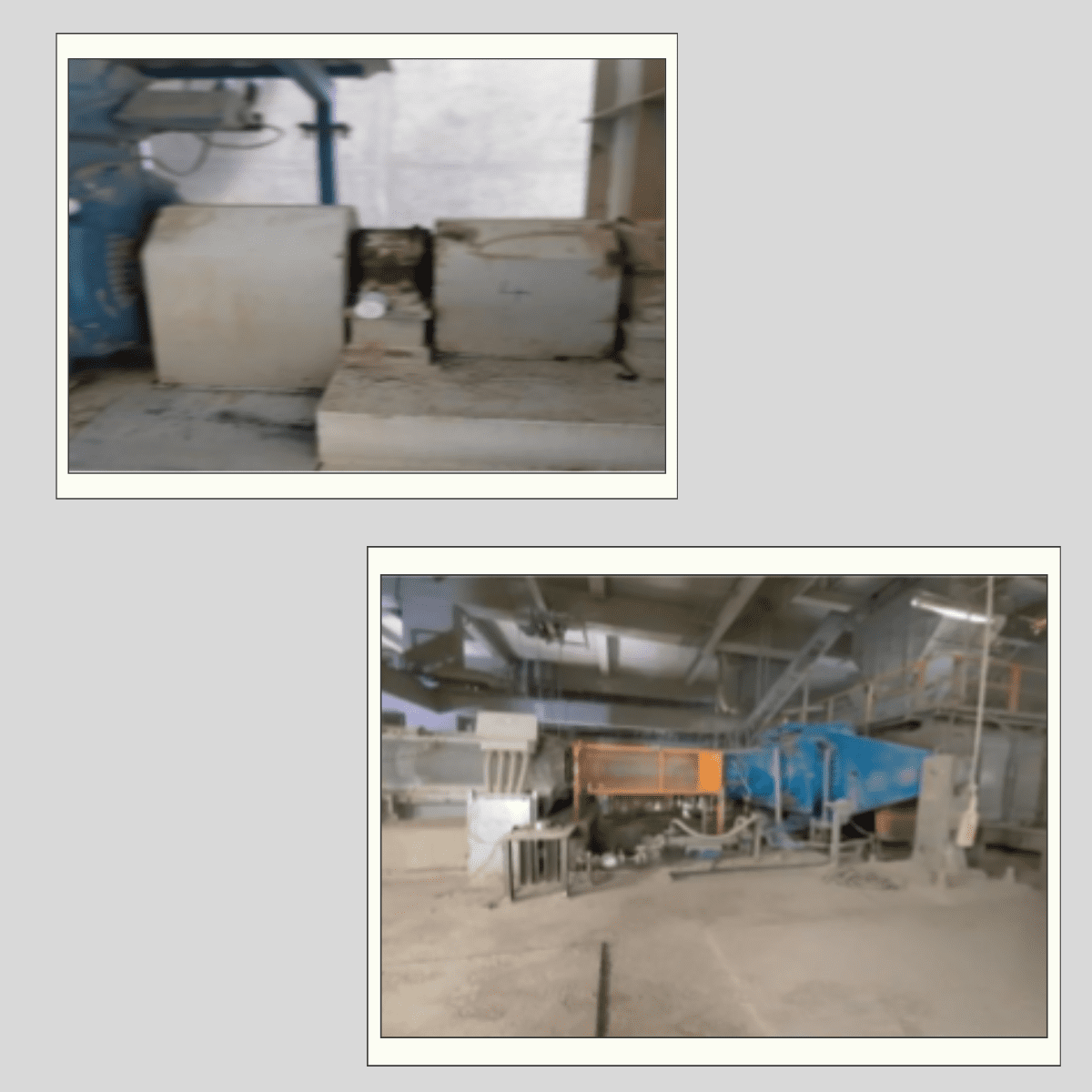
ASSETS COVERED
FAULTS DETECTED
Challenges
- Managing assets distributed over a large manufacturing facility makes daily data collection from each asset a challenging and time consuming task.
- Reduce the vibration analyst time spend on analyzing data coming from reliable and healthy machines. Most machines are reliable ~60% of the time and there is hardly any change in data or spectrum, analyzing the same healthy data can lead to data fatigue
- Low consistency and repeatability in collecting vibration and other condition data can lead to difference in interpretation and trending.
Outcomes
- ioEYE Predict collects vibration and ultrasonic sensor data wirelessly without the need to visit these assets. The monitoring and inspection of each asset have become significantly easier.
- ioEYE utilizes vibration and acoustics sensors that collects data at regular intervals, with AI algorithms predict potential failures in the assets. The vibration analysts now spend their valuable time in inspecting spectrums and assets flagged by the AI system. This has helped Yamama expand their reliability program to more number of assets without creating additional workload for the reliability team.
- ioEYE Predict sensors are permanently fixed on the assets. This ensures that data is recorded consistently without the location and data capture errors creeping into the measurements.
Revolutionizing Reliability: Unleashing the Power of Digitization 4.0 for plant maintenance.
Yamama is a leading player in the cement industry. It faced significant challenges in monitoring and assessing reliability across their expansive field of assets. They had been using predictive maintenance since some years and it had proven very effective in improving reliability across their assets. They wanted to expand it across larger number of assets without compromising on the quality of their inspection and analysis. But expanding the program across larger number of assets with the same team had its own challenges.
Yamama explored various technologies with the vision to expand predictive maintenance and reliability program. They finally chose an AI and IoT sensors driver approach as it solved their two critical problems – time spend on data collection and second the time spend on analyzing data from healthy machines that had no issues.
After a detailed evaluation of suppliers they chose SenseGrow’s ioEYE Predict solution. They carried out a pilot and a detailed evaluation of the battery life, wireless communication, data accuracy and prediction capabilities. The ioEYE Predict wireless sensors, ease of installation and AI accuracy was the winner.
Yamama chose to install the entire system themselves. The ease of installation of the system allowed them to could retrofit their assets without any major shutdown or hot work. No communication or power cables were needed to be run. They used IoT gateways with a SIM card to provide the sensors connectivity to the ioEYE predict cloud. Since the system was not infringing or connecting with any of their IT systems it ensured high security through isolation.
With the implementation of ioEYE Predict, monitoring and inspecting each asset became a seamless process. The vibration and ultrasonic sensors, strategically placed on assets, ensured accurate data collection at regular intervals. This not only addressed the accuracy issue faced during manual data collection but also provided a continuous stream of reliable asset health information.
Furthermore, ioEYE Predict’s advanced AI algorithms, fueled by historical data, enabled Yamama to predict potential failures with unparalleled precision. The system’s predictive maintenance capabilities allowed them to proactively address issues before they escalated, minimizing downtime and optimizing asset performance.
In conclusion, Yamama’s adoption of ioEYE Predict marked a transformative turning point in their operations. The challenges of manual data collection and the overwhelming task of inspecting numerous assets were effectively overcome. With ioEYE Predict, Yamama not only streamlined their monitoring processes but also elevated their ability to predict and prevent asset failures, ultimately enhancing their overall reliability, efficiency and success in the cement industry.
“We have installed condition monitoring system from SENSEGROW for 3 cement mills at Yamama Cement company. Wireless monitoring system is very simple and easy for installation and the data is very much reliable. SenseGrow predictive Dashboard is very much user friendly and having all parameters and measurement tasks. Each triaxial sensor has many measurement task other than vibration, it measures Ultrasound, thermal analysis, magnetic flux analysis. Reports are generated instantly and there is good feedback from staff for any queries”
Sayed Masood
INSPECTION SUPERVISOR
Explore the products which help our customers grow
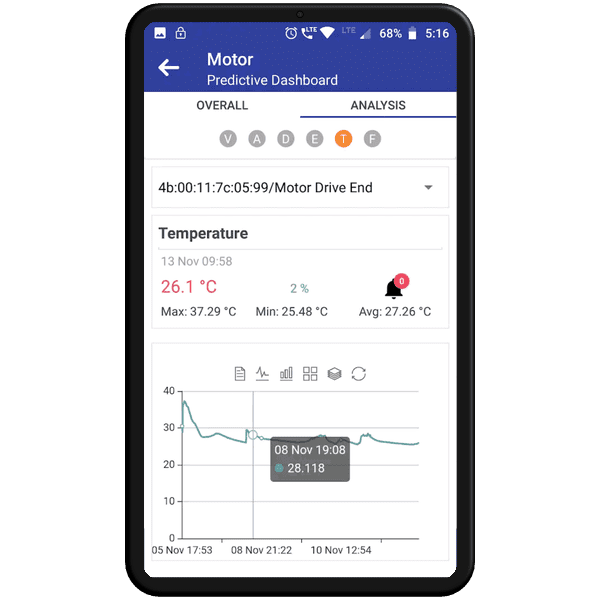
AI and cloud platform for predictive maintenance
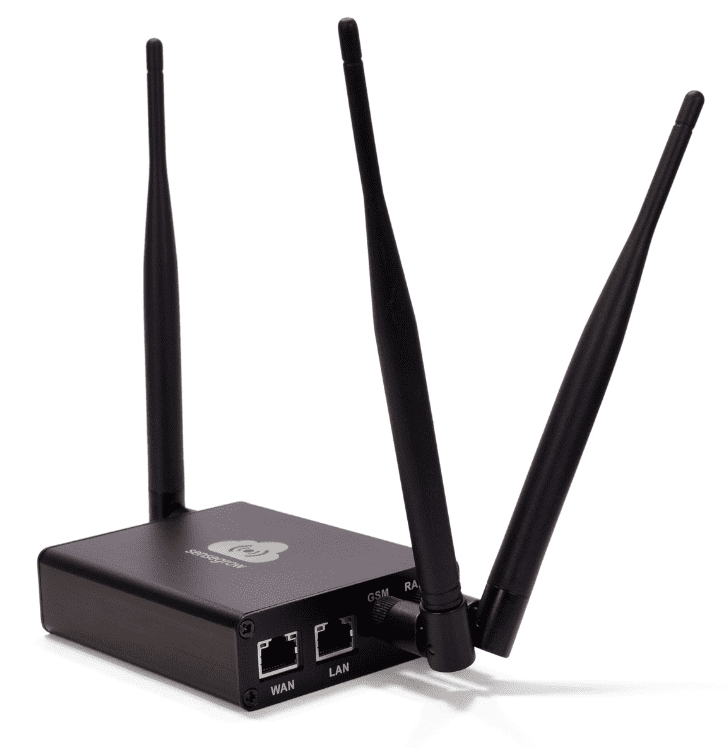
IoEYE Predict Gateway
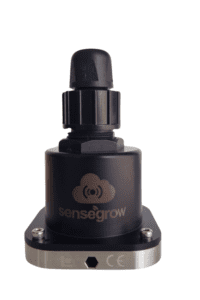