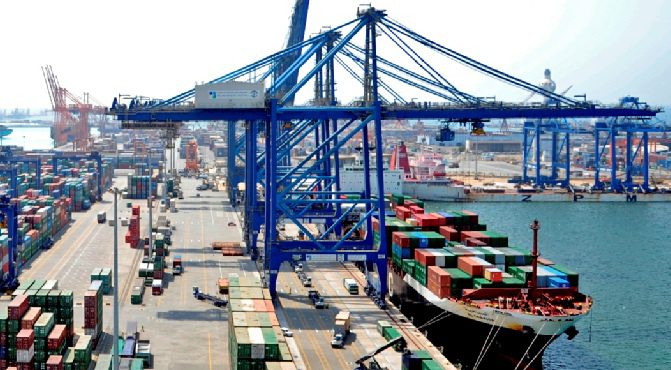
Red Sea Gateway Terminal was established in 2009 as Saudi Arabia’s first private sector Build-Operate-Transfer project. Currently, with an annual container throughput capacity of 5.2 million TEUs, RSGT is providing world-class integrated logistics solutions, port operations in one of the world’s 40 busiest container ports and serves as an engine of growth for both local and regional economies.
crane maintenance
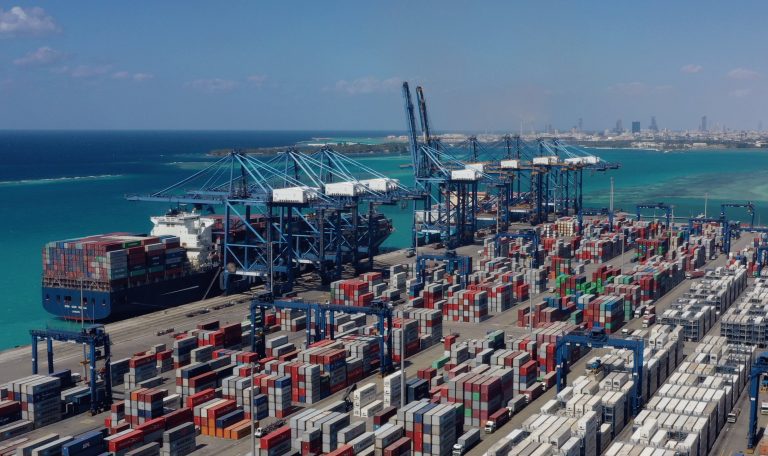
INDUSTRY
Shipping and Port Operations
COMPANY SIZE
$127 million
YEAR FOUNDED
2009
KEY USE CASES
Improve super panamax quayside container crane crane reliability by leveraging IoT, Machine Learning (ML) and Artificial Intelligence (AI) for real-time condition monitoring and fault predictions.
PRODUCTS & INTEGRATIONS ioEYE Predict Sensors
ioEYE Predict Predictive maintenance AI Cloud
Azure AD directory.
24
World’s largest quay cranes
32%
Reduced inspections
83%
Accuracy of faults predicted
19 %
Overall reliability improvement based on increase in MTBF
Enhanced reliability with predictive and condition monitoring for gantry cranes leads to higher annual throughput of containers at the terminal. In container port operations reliability of gantry cranes is very important as an unplanned breakdown can lead to vessel and cargo delays.
- Reduced inspection
- Higher MTBF (Mean Time Between Failures)
- Higher uptime and availability
- Autonomous crane monitoring and fault detection and prediction contribute to saving maintenance team time
crane maintenance
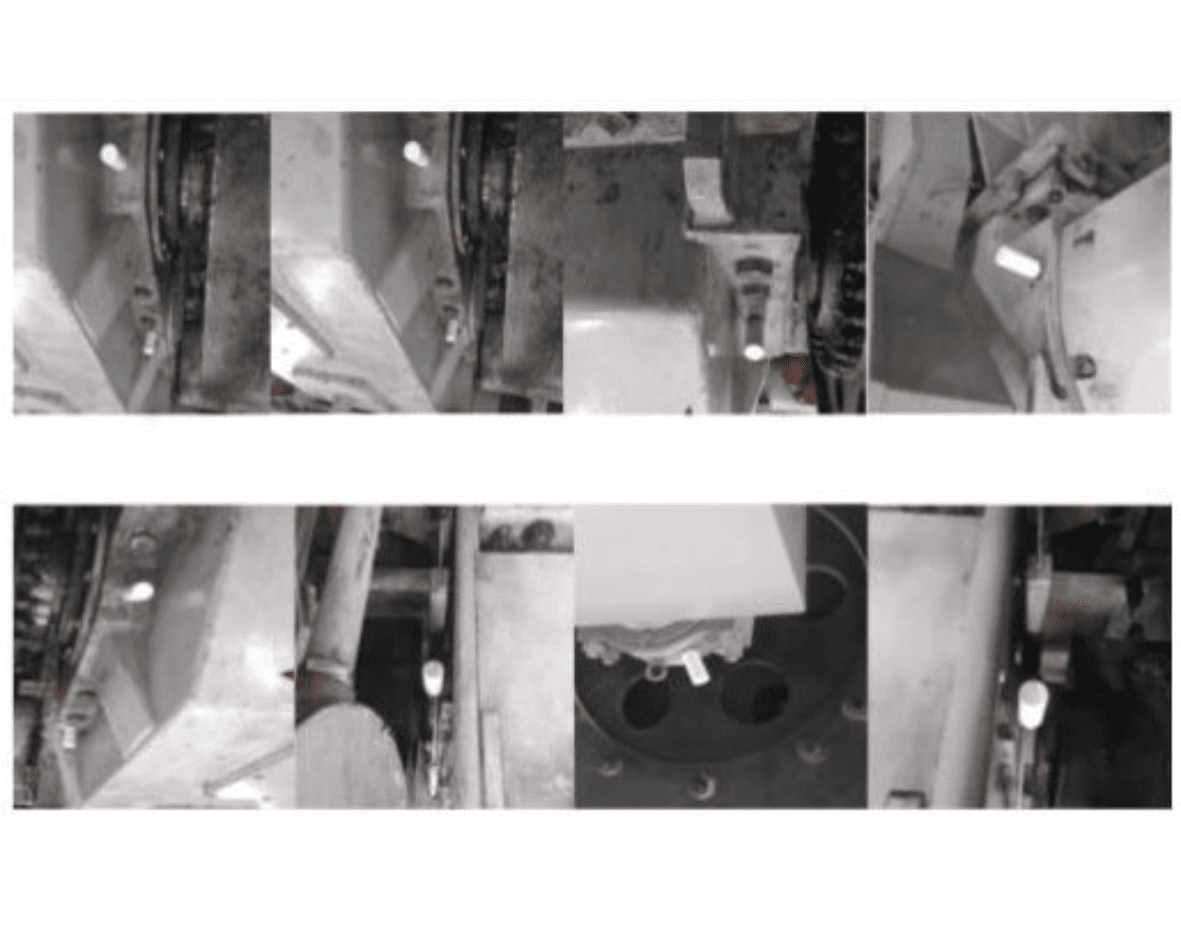
ASSETS COVERED
Super Panamax Cranes QC05 LS hoist drive
CRITICAL COMPONENTS MONITORED
Challenges
- The challenge of inspecting multiple Super Panamax cranes at various locations, especially when most of them are being operated round the clock.
- Maintenance was primarily done in a planned schedule, but there was no way to know or assess the reliability and condition of the cranes. Proactive predictive maintenance, in case of a fault developing, was not possible due to lack of crane data.
- Accessing certain parts of the cranes for inspection might involve working at heights or in confined spaces, posing safety risks for inspection personnel.
- Most motors and gears of the crane only operate for short intervals and at variable RPM during container loading and unloading operations. Collecting reliable data was a challenge due to this intermittent, variable load and variable RPM scenario. Even with a hand held the vibration engineer had to wait for long durations to capture the right vibration spectrum data. For some gearbox shafts the RPM was very low and low amplitude vibration signatures were lost in instrument noise floor.
Outcomes
- After implementing the ioEYE solution the complexities of inspecting multiple super panamax cranes at various locations was resolved and it also resulted in a more efficient, safe, and cost-effective maintenance inspections.
- The solution enabled capturing the leading indicators of machine failure like vibration, ultrasound and temperature. The ML and AI models were able to indicate machines that were developing an anomaly and also predict or detected the exact faults. This allowed proactive predictive or condition based maintenance of gantry cranes and reducing their unplanned downtime.
- By leveraging remote monitoring, and machine reliability, the need for personnel to work at heights has been minimized. This ensures a safer working environment, reduces the potential for accidents, and enhances overall safety measures during crane inspections.
- SenseGrow implemented a special provision to take care of these intermittent and variable load/rpm scenarios. This allows autonomous data collection at a time when data accuracy could be ensured. This quality and event driven data capture allowed acquisition of high quality spectrum data. SenseGrow deploys a combination of ultrasound, magnetic flux and vibration sensors and a reinforced learning AI model that makes predictions in such variable RPM and load conditions possible.
Revolutionizing Crane Asset Management with ioEYE Predict Solution
Red Sea Gateway Terminal (RSGT) stands for excellence in the sector of marine industry and logistics, strategically positioned at the crossroads of global trade. Established to meet the evolving needs of the shipping industry, RSGT has become a key player in facilitating efficient and seamless cargo movements through its state-of-the-art terminal.
RSGT’s terminal, located in Jeddah Islamic Port, Saudi Arabia, is equipped with cutting-edge technology and world-class infrastructure. The terminal has a handling capacity of 2.5 million TEUs (twenty-foot equivalent units) annually, making it one of the largest container terminals in the region.
crane maintenance
RSGT’s dedication to innovation, reliability and commitment to excellence motivated the RSGT maintenance team to innovate around how super panamax cranes are maintained. The objective was to improve crane reliability and eliminate downtime, which would lead to higher annual container throughput. RSGT maintenance team was one of the first to envision using AI for predictive maintenance of wheeled gantry cranes. Not an easy task but the team was determined and highly motivated to make it possible.
“RSGT is committed to adopting innovative technologies to digitize it port operations for higher reliability and efficiency”
The RSGT company faced multiple challenges in maintaining their Super Panamax cranes. However, with the implementation of the ioEYE Predict solution, they embarked on a transformative journey towards overcoming these difficulties. The solution’s predictive algorithms and real-time monitoring capabilities streamlined the inspection process, enabling the definition of accurate maintenance times with precision. Manual condition monitoring data collection with handheld vibration meters was was replaced with a system that collected data autonomously. This saved man-hours that were spend on data collection. The vibration engineers were spending less time on climbing these cranes for data collection and spending that time in deeper analysis & continuous improvement. Safety concerns of working at these heights were also reduced through remote monitoring and machine reliability, creating a safer working environment and enhancing overall safety measures during super panamax crane inspections.
The ioEYE Predict ML and AI system worked as a decision support system for the maintenance engineers. The system was able to analyse all the spectrums and data that was generated and then able to pinpoint spectrums that had a high probability of a fault developing. It then flagged these assets to the vibration engineer via an email who would then analyze them in depth. This allowed condition analysis on a daily basis instead of the route based monthly interval. Any faults that were confirmed, rejected on identified by the vibration engineer were captured in the system and was later used by the system to improve its performance.
The ioEYE Predict solution also provided RSGT with valuable data insights that were previously unattainable. The system collected multiple data on RPM, run hours, MTBF, MTTR, etc. and allowed for better decision-making on maintenance schedules. By analyzing this data, RSGT was able to identify trends and patterns that helped them optimize their operations, reduce downtime, and increase productivity. For SenseGrow team too this was a challenging and first of its kind problem to solve.
In addition to the practical benefits, RSGT also saw a positive impact on their bottom line. The reduction in downtime and maintenance costs, as well as the increased productivity, resulted in significant savings for the company. The investment in the ioEYE Predict solution proved to be a wise decision, not only improving the efficiency of their crane asset management but also increasing their profitability. Lower down time and more reliable cranes means higher container throughput and increased revenue.
Overall, the implementation of the ioEYE Predict solution revolutionized RSGT’s super panamax crane asset management. By leveraging the power of predictive algorithms and remote monitoring, RSGT was able to optimize their operations, enhance safety measures, and increase reliability. The success of this implementation demonstrates the significant impact that technology can have on traditional industries, paving the way for continued innovation and progress.
With ioEYE Predict, crane reliability and asset management has been transformed into a futuristic, IA driven and hassle-free process. The solution has enabled the company to achieve greater efficiency, safety, and cost-effectiveness in managing its cranes.
crane maintenance
Explore the products which help our customers grow
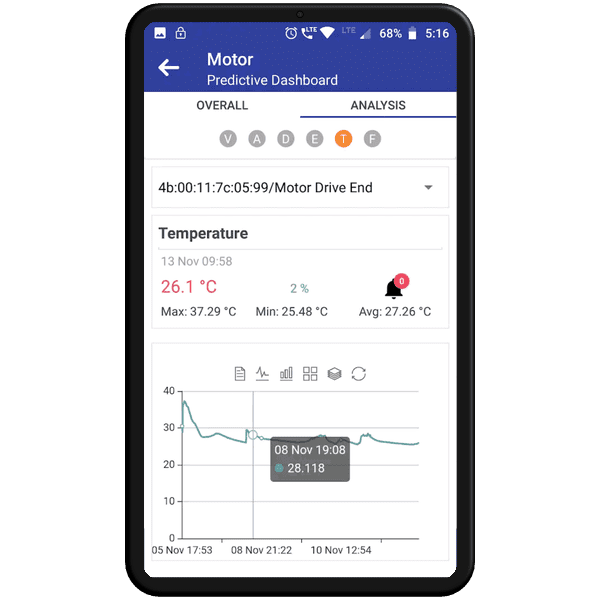
AI and cloud platform for predictive maintenance
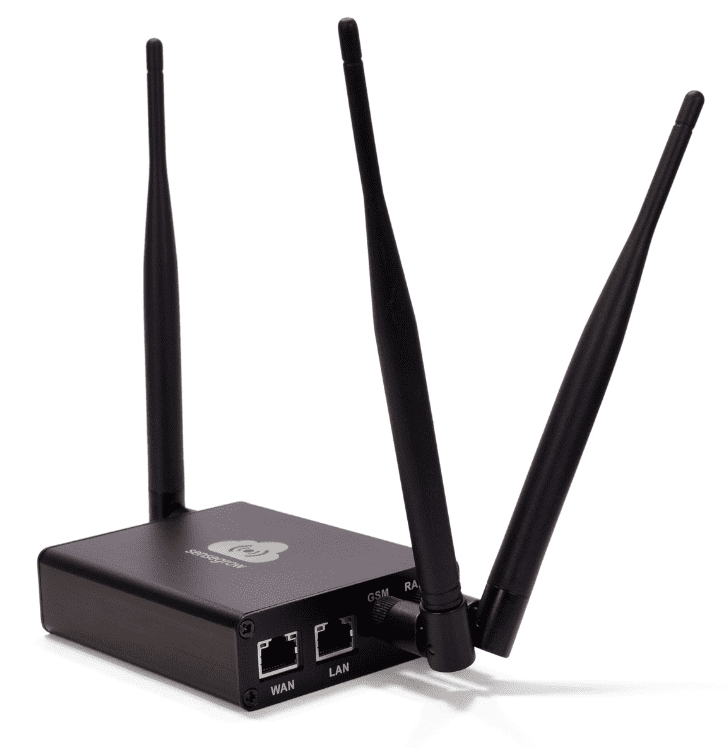
IoEYE Predict Gateway
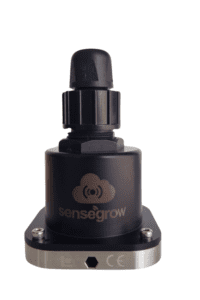