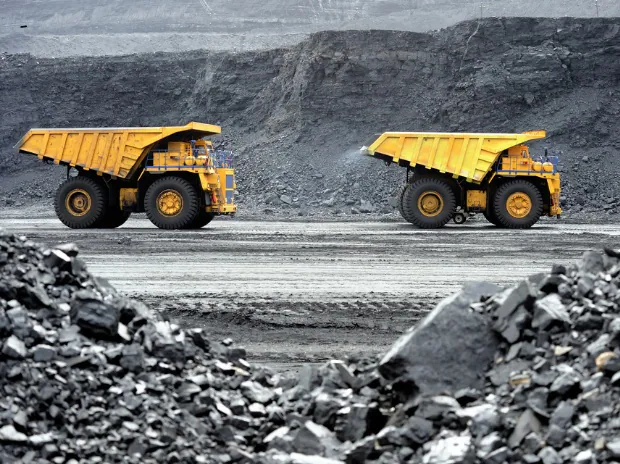
Minning secures innovation
Creating Value Touching Lives
Essel Mining & Industries Limited (EMIL) is one of the oldest mining companies in India. Operating since 1950, EMIL has expanded its business into coal mining, diamond mining, Noble Ferro Alloys, iron pellets and renewable energy. It has 12 sites across 6 states with a experience of 72+ years.
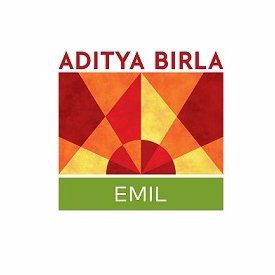
INDUSTRY
Mining
COMPANY SIZE
500-1000 employees
YEAR FOUNDED
1950
KEY USE CASES
Improve asset reliability by leveraging IoT and Artificial Intelligence (AI) for real time condition monitoring and fault prediction.
PRODUCTS & INTEGRATIONS
ioEYE Predict Sensors
ioEYE Predict Predictive maintenance AI Cloud
Azure AD directory.
36%
Overall reliability improvement based on increased in MTBF & Uptime
5
Large Critical assets monitored
7
Faults Predicted
21%
reduction in unplanned downtime
- Improved reliability that lead to reduced capital and operating expenditure:
- Increased asset life due timely intervention to reduce accelerated ware – leading to lower capital expenditure in asset replacement.
- Timely corrective action leads to higher MTBF reducing maintenance costs.
- Autonomous monitoring and prediction save maintenance team time spend on inspections and data collection. Manual inspection frequency has been reduced by almost one third.
- Higher and more predictable productions: Higher reliability leads to reduced unplanned downtime. This enabled less unexpected stoppages in production.
Challenges
- Mining operations are often located in remote or hazardous environments, where manual maintenance tasks expose workers to physical dangers, and exposure to harmful substances.
- Manual inspections and reliability assessments requires significant work hours, which can strain maintenance team resources and increase operational costs.
- Decisions like detailed inspection or repair can be difficult to make in lack of machine condition data. Without data it can also be very difficult to detect issues early enough, resulting in more extensive and costly repairs.
- Machineries were in locations where there was not IT infrastructure. It was difficult to transmit data to the software. Laying an IT network was not an option.
Outcomes
- With ioEYE Predict solution the maintenance team can now remotely monitor the assets health from a mobile or desktop.
- ioEYE Predict predictive maintenance solution automates data collection and reliability assessment of monitored assets. This reduces work hours spend on inspections and decision making.
- The vibration and ultrasonic sensors capture issues at a very early stage with consistently high accuracy. This data is autonomously analyzed by ioEYE Predict AI predictive maintenance models. In case of issues it sends out alerts to the maintenance team to do detailed, data driven, root cause analysis and take corrective action.
- A wireless sensor network and GPRS backbone to sent the sensor data to the ioEYE Predict cloud eliminated the need for an IT network near these machines.
Solving Machinery Huddles with AI
The 72+year-old company “Essel Mining & Industries Limited” was founded in 1950, it holds a legacy of innovation and growth. EMIL has expanded its business into coal mining, diamond mining, Noble Ferro Alloys, iron pellets and renewable energy.
The company operates manufacturing facilities across India, equipped with hundreds of rotating and reciprocating machinery. During its inception, the company was only dealing with iron ore and Manganese mining. Subsequently, it forayed into Nobel Ferro Alloys manufacturing. In 2012 for the first time it took up the challenge to operate a coal mine of Government of India on MDO mode.
EMIL since last few decades have been using a mix of planned, condition based, reactive and protective strategies to maintain and protect its machineries. Technicians would routinely inspect each machine, looking for signs of wear and tear, hoping to detect any potential issues before they escalated into costly breakdowns. For critical machineries they use vibration handheld that provide overall vibration measurements. They are also using vibration, displacement and temperature switches for protecting machineries from absolute catastrophic failure. However, this approach came with its own set of challenges and limitations.
As one of the leading mining industries in India, Essel Mining has always prided itself on reliability and efficiency. Still, the manual inspection and maintenance process was resource-intensive and lacked data driven decisions. Protective systems could only protect the machines and not prevent unplanned downtime. Technicians would spend hours meticulously inspecting agitator blades, shafts, bearings, seals, and gaskets, with their keen eyes and years of experience. Yet, despite their dedication, the company encountered many challenges such as Mechanical Wear, Seal and Gasket Failure, Motor or Drive System Issues, and Belt Tension and misalignment Problems. Downtime due to unexpected breakdowns was a constant concern.
The situation called for a transformative solution. After careful research and evaluation of digital reliability solution, and they chose SenseGrow. What swing their decision towards SenseGrow was the user experience and accuracy of our predictive maintenance software. Essel Mining implemented ioEYE Predict Vibration Sensors in five of their crucial assets which covered 12 major components that failed often.
With the ioEYE Predict sensors in place, real-time monitoring became possible without additional man hours being spent on data collection and inspections. These sensors continuously tracked the vibrations, temperature, ultrasound, and other vital data of these assets. When anomalies were detected or faults predicted, the system would instantly alert the maintenance team over email.
The team would then analyze the predictions made by the AI and the data on which these predictions were made. They would combine the analysis with more contextual information like process, operating conditions etc. and do a root cause analysis. They then decide on the course of action to rectify it or mark it as no risk fault for the AI to learn from this feedback.
This shift from manual checks to predictive maintenance was a big relief for the maintenance team and also lead to improved reliability across their assets.
“SenseGrow remains dedicated to our continued collaboration with Essel Mining & Innovation (Aditya Birla Group), aiming to provide inventive solutions that not only improve machine reliability and efficiency but also foster long-term sustainable expansion of their AI driven predictive maintenance decision support system“
“The solution is reliable and easy to use. Sensegrow Predictive Maintenance Solution solved the unplanned downtime challenge for us.”
Jyoti Ranjan Behera
IT & DIGITAL
AI AND SMART SENSORS FOR PREDICTIVE MAINTENANCE
Choose a new and better way to maintenance.
Explore the products which help our customers grow
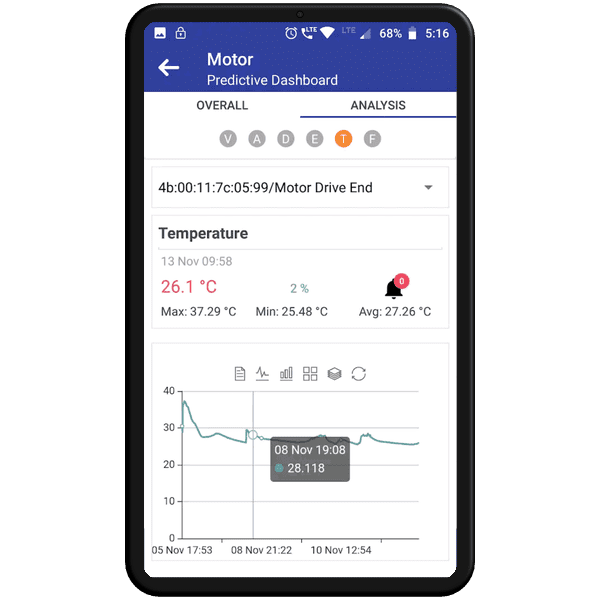
AI and cloud platform for predictive maintenance
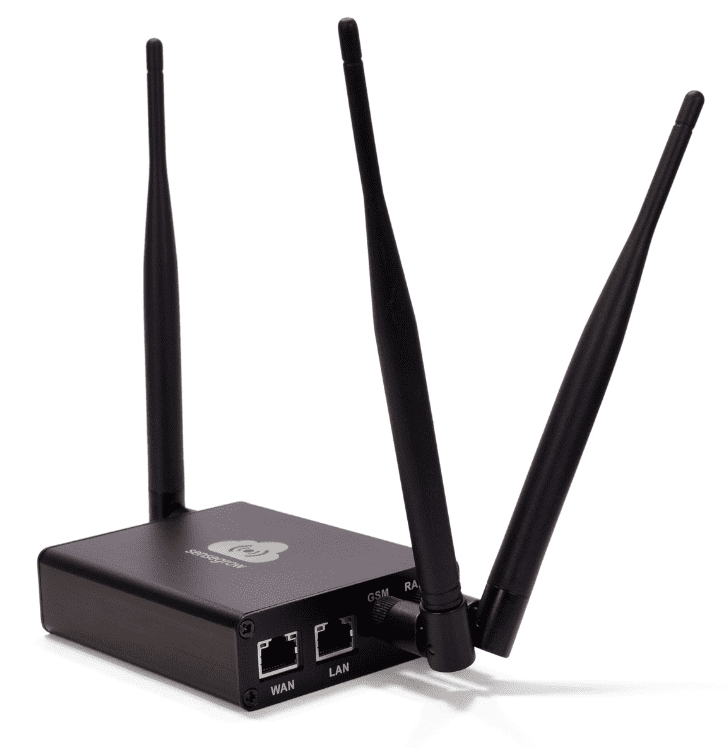
IoEYE Predict Gateway
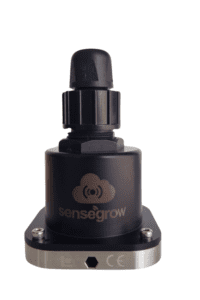