Industrial Maintenance And Its Types: An Overview
In this article, you will know about industrial maintenance and various types of maintenance strategies that are used in manufacturing industries. Moreover, we will see what maintenance strategy to choose based upon the priority or criticality of industrial assets.
What is Maintenance?
As we are looking into industrial maintenance here, the technical meaning of industrial maintenance is to inspect for faults inside assets or equipment and perform the repair or maintenance function if found necessary.
The maintenance work can be performed on either a full machine failure or otherwise which forms the basis of different types of maintenance described below.
What are some common Types of Maintenance strategies?
There are mainly 4 types of maintenance strategies that are used inside the manufacturing plants, namely – Reactive Maintenance, Preventive Maintenance, Condition Based Maintenance, and Predictive Maintenance.
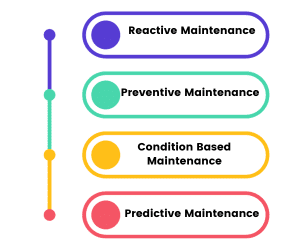
1. Reactive Maintenance:
Reactive Maintenance, as the name suggests, is performed when a failure has already occurred.
As a strategy, this may be unavoidable no matter how well defined your maintenance strategy is because, despite all efforts, failures do occur.
While this approach has glaring disadvantages such as surprise repair costs, shorter asset life expectancy, and safety issues, it does have some advantages as well.
A reactive maintenance approach is suitable when you are not operating any critical systems and have plenty of redundancies.
This way the startup costs are much lower and due to a lower requirement for maintenance staff the company can offer competitive rates to their customers.
Read more on Reactive Maintenance.
2. Preventive Maintenance:
Preventive Maintenance is the most common, or say the prevalent type of repair work done inside the industries.
Everyday life in factories and even in people‘s lives depends on many systems and machines. Some of them are mundane enough that we don’t notice until they fail, while others are very critical and require a constant operation.
For ordinary or non-critical systems, the consequences of failure might just be an inconvenience. For such systems fixing the problems as they happen (Reactive Maintenance) is usually acceptable. As systems become more critical, regular preemptive maintenance is usually performed.
To that effect, industries have been relying on Preventive Maintenance techniques. Although the exact details of Preventive Maintenance vary based on the equipment, it involves periodic inspection, evaluation, and repair/replacement of parts to prevent failure. Typical activities in a Preventive Maintenance schedule involve cleaning, oil changes, adjustments, and sometimes an overhaul.
This determination to replace parts is either based on the condition of the parts after an inspection or just based on the manufacturer-recommended life cycle (in hours of operation). This sacrifices the factory owner’s ROI with the assurance that short-term loss is better than a catastrophic failure. As true as that might be, there is still a non-zero chance of failure. Which then begs the question, is sacrificing ROI for a non-zero chance of failure worth the cost if and when that eventuality happens? Clearly, this practice greatly mitigates the chances of failure but results in wasted resources.
Despite the risk of ROI, there are some obvious benefits to using Preventive Maintenance, such as:
· Finite equipment operational life
· Fewer equipment failures
· Better visibility of maintenance schedules
Read more on Preventive Maintenance.
3. Condition Based Maintenance
Condition Based Maintenance (CBM) is the type of maintenance rely on the actual condition of the asset rather than on predefined maintenance schedules. These systems are considered more cost-efficient because they focus maintenance activities on equipment that shows signs of deteriorating performance or upcoming failure thereby increasing the time between maintenance repairs. The indicators for performance can be gathered in multiple ways including visual inspections, periodic spot measurements, and sometimes continue through the use of sensors.
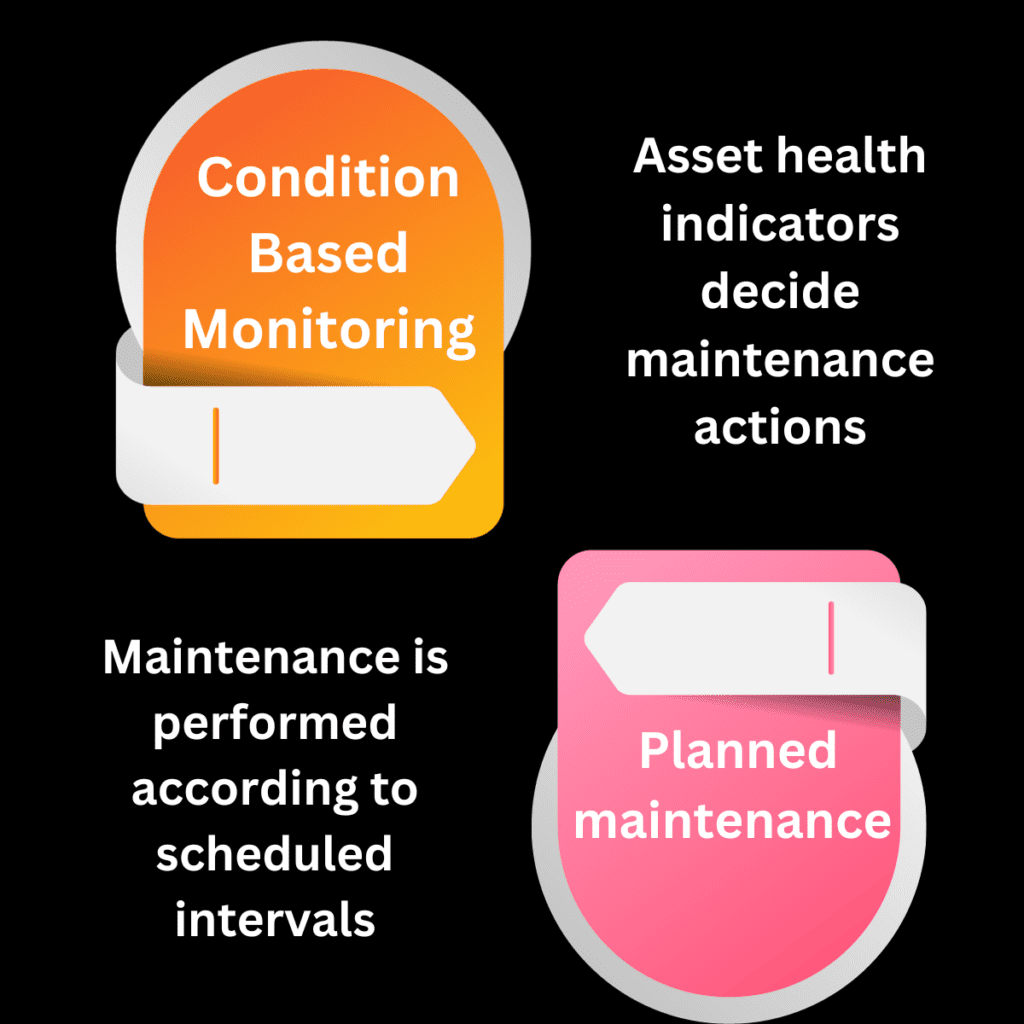
The fundamental goal of Condition Monitoring Systems is to schedule maintenance when they spot an upcoming failure and not because a certain amount of time has elapsed since the last maintenance. This approach, however, has some of the same challenges that Predictive Maintenance Systems could suffer from, as we outline later in this post.
4. Predictive Maintenance
In recent years Predictive Maintenance has generated a lot of interest both from maintenance solution providers and customers alike.
Predictive Maintenance relies on sensor data to determine the probability of failure before it happens. Current solutions are leveraging Machine Learning models to analyze the various types of data generated by factory machines. This data is then used to determine the state of the machines and attempt to predict failures. This approach does yield promising results and new developments in the area of machine learning are making predictions even more accurate.
Predictive Maintenance solutions seem even more relevant considering the cost of failure for critical equipment. Imagine having to shut down production because one of the critical systems broke down unexpectedly and in between scheduled maintenance windows. The cost of failure is not just in terms of lost production but also involves various other costs such as:
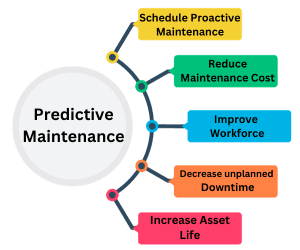
· Cost of pulling maintenance crew to work on this work order which in turn delays their current tasks.
· If the maintenance crew is unavailable or unable then it can be prohibitively expensive to involve outside contractors for repairs.
· Parts for such critical equipment have to be maintained in the inventory in excess.
· If parts are unavailable at the time then procuring them for this work order would also require an expensive shipment.
So, overall, the cost of failure is so prohibitive that factory owners would rather risk the loss of value in replacing parts with Preventive Maintenance than risk an unexpected failure.
When used optimally, Predictive maintenance can lead to significant cost savings with better predictability and of course increased operational times of the systems.
Read more on Predictive Maintenance.
Which is the best among all these maintenance types?
Final Words
So this was an overview of industrial maintenance practices.