Machine failure is common to the works. Machine breakdowns will price loads. To resolve the upkeep strategy like reactive, prognostic & preventive maintenance square measure used.
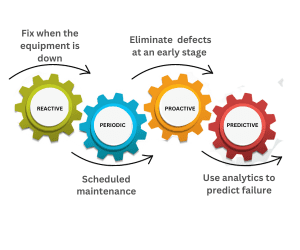
Reactive Maintenance:
Known as breakdown maintenance, it’s straightforward maintenance is completed once breakdowns occur. there’s a sudden breakdown. Maintenance isn’t pre-plan of the breakdown. that the ending of the plant price loads.
Preventive Maintenance:
If you wouldn’t wait till your automobile engine fails to induce the oil modified, then you already grasp the worth of preventive maintenance. Be regular for maintenance performed on an everyday basis to scale back the probability of failure is preventive maintenance.
Also typically referred to as planned maintenance, preventive maintenance is conducted throughout Associate in Nursing asset’s traditional operative conditions. This helps avoid sudden breakdowns and their expensive consequences, like unplanned period of time period of time.
Predictive Maintenance:
Predictive Maintenance starts with knowledge assortment. this is often usually accomplished by attaching detectors to mill instrumentation and networking them to transmit this sensor knowledge. This knowledge is then analyzed for anomalies and therefore the likelihood of failure is decided in time period. the longer-term health of kit will then be foretold so as to alter on-demand maintenance
Latest Tech by SenseGrow is designing that the common price of unplanned machine period of time is reduced by 70-80%. that price around $290,000 per hour. Total calculation over the year is available in billions of greenbacks.
Most of producing plant has seen quality failures & unforeseen repair prices. Their square measure perpetually some belongings you can have to be compelled to look to frequent machine downtimes:
- Poor instrumentation maintenance
- Ambiguous job directions
- Human error
- Lackadaisical changeovers
- Early shutdowns
- Frequent personnel breaks
- Long set-up time
- On-machine press checks
- Lack of period of time knowledge recording
However, these square measure simply causes; the results is way more unfortunate. as an example, the unplanned machine period of time will offset your producing productivity by many days or lead you to the subsequent setbacks:
- Increased repair price
- Delayed production
- Overall instrumentation effectiveness
Not to mention that these setbacks can inevitably lead to the raised total price of possession (TCO) and low production price. But there’s hope. Most of the producing plants have started victimization prognostic maintenance systems to boost overall instrumentation effectiveness & scale back overhead maintenance prices to avoid production delays.