ESP, is an efficient and reliable artificial-lift method for lifting moderate to high volumes of fluids from wellbores. ESPs are widely used in the oil and gas industry to lift fluids from the reservoir to the surface. ESPs are also used in water applications, such as irrigation, municipal water supply, and groundwater remediation. ESPs offer several advantages over other artificial lift methods, such as lesser footprint, high flow rates, available downhole telemetry, easy installation and operation etc. ESPs can handle a wide range of fluid properties, such as density, viscosity, gas-liquid ratio, and solids content. ESPs can also operate under different reservoir conditions, such as temperature, pressure, and depth.
However, ESPs are also subject to various failure modes due to harsh operating conditions. Average electric submersible pumps (ESP) runs to failure in just 2-3 years. Failure is often unexpected, making it difficult to replace the ESP in a short time frame. ESP failures can result in significant production losses, increased operational costs, and environmental risks. Therefore, it is essential to monitor and maintain ESPs to ensure their optimal operation and reliability.
What is the working principle of ESP?
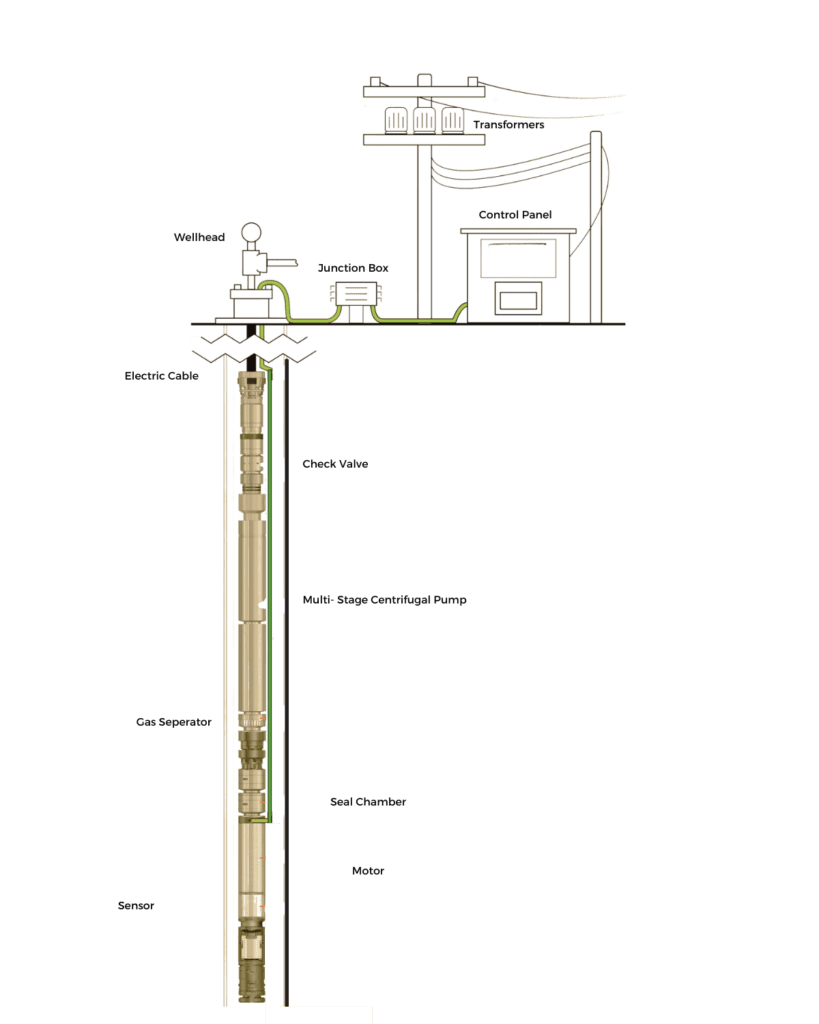
ESP’s main components include:
- Multistage centrifugal pump
- Three-phase induction motor
- Seal-chamber section
- Power cable
- Surface controls
The components are normally tubing hung from the wellhead with the pump on top and the motor attached below.
The motor rotates the shaft which is connected to the pump through the seal-chamber. The shaft is designed to be as small in diameter as possible without compromising its strength which allows greater volumes to pass through the pump intake. The pump intake is where the well fluid enters the submersible pump and is directed into the impellers. Different types of intakes are used depending on fluid properties, particularly the gas-liquid ratio (GLR). Standard designs do not separate gas and are therefore used in wells that produce a very low gas-to-liquid ratio. To separate gas in a well stream with relatively high GLR, either a reverse-flow or rotary pump intake is used.
The centrifugal pumps are multistage and pressure of the fluid is increased at each stage successively. The stages are made up of rotating impeller and stationary diffuser. The stages can be stacked to incrementally increase the pressure until the desired flow rate is achieved. The fluid travels through a rotating impeller which increases its kinetic energy, or velocity. It then enters the diffuser, converting the energy to potential energy which raises the discharge pressure. This operation will continue until the fluid reaches the design discharge pressure. The increase in pressure is called the total developed head (TDH) of the pump.
Common challenges associated with ESP operation:
ESP failures in Oil Wells can be grouped into three main categories namely electrical failures, mechanical failures and operational failures
Electrical Failures: Typically the weakest link in an ESP system, most failures are electrical, usually resulting from a mechanical problem as the underlying cause of the failure. Increased downhole pressure and temperature often induce surface system failures by straining the electrical supply, resulting in failure of electrical components.
Mechanical Failures: Difficult to remedy and usually require component retrieval and replacement. E.g. component breakage, corrosion, dislocation, and leakage. Mechanical wear can lead to reduced efficiency, increased power consumption, and leakage of the fluid or oil.
Operating Failures:
- Temperature: High temperatures causing failures of electrical components that cannot handle the temperature conditions. The most affected electrical components include the cable and downhole sensor.
- Pressure: Sudden surge or sudden loss in pressure. A sudden surge in pressure can result from a fluid influx such as a gas pocket. A sudden decrease in pressure can result from leakages in the ESP assembly. In both cases, abnormalities in the flow will occur. If the system is not fast enough to adapt to the changes, the downhole equipment may be degraded.
- Multiphase: The most common fluids associated with the oil are water and gas. Water can cause system overload if the water cut is extremely high. Also, water–oil viscous emulsions can be extremely problematic during production. The gaseous phase can also cause severe problems. These include corrosion, gas lock, and a surface kick. If gas problems occur, such as gas lock, operations must be stopped until the excessive gas is vented.
- Gas locking: This is the accumulation and trapping of the free gas in the pump, which can reduce the effective liquid volume and the hydraulic force. Gas locking can lead to reduced flow rate, increased power consumption, and cavitation of the pump.
- Scale/Solid Deposition
- Pump-off conditions
- Deviated Wells
Some of the common problems that affect the performance and reliability of ESPs in water applications are:
- Electrical faults caused by overvoltage, undervoltage, overcurrent, or short circuit of the power supply, which can damage the insulation, windings, and connectors of the motor and cable.
- Corrosion due to presence of water, oxygen, carbon dioxide, hydrogen sulfide, or other corrosive agents, in the water or oil, which can form acidic or sulfide compounds that can attack the metal surfaces. Corrosion can also be caused by the galvanic action.
- Scaling due to deposition of mineral salts, such as calcium carbonate, calcium sulfate, or barium sulfate, on the pump and tubing surfaces.
Impact of ESP failures:
Most ESPs are in remote locations and it’s also difficult to repair or replace them. Failure can take up to 6 months to repair and can be costly. The failures can result in:
Production losses: ESP failures can reduce or stop the production of fluids from the well, leading to revenue losses and contractual penalties.
Operational costs: ESP failures can increase the operational costs associated with repairing or replacing the system, as well as the costs of interventions, workovers, and rig operations.
Environmental risks: ESP failures can pose environmental risks due to the leakage of fluids or chemicals into the surrounding area, causing soil and water contamination, greenhouse gas emissions, and fire hazards.
Current Solutions and Limitations:
Traditional maintenance strategies often involve scheduled maintenance or reactive approaches, leading to inefficiencies and increased downtime. Due to enormous costs of ESP failures, operators are progressively investing in real-time monitoring systems that use the downhole data to track it’s performance and provide alerts for tripping or failure occurrences. Unfortunately, downhole sensors often fail leaving operators blind.
Our Experience:
We at SenseGrow Inc have experience of working with more than 1000+ Electric Submersible Pump data captured in Oil Well and Water applications. The electrical signature of the motor is one the easiest to monitor in ESP applications as it is difficult and costly to install other sensors on the submersible pump. Electrical Signature Analysis only requires installation of CT (Current Transformers) for current and voltage taps for voltage signature. We have come across the following two scenarios:
- Model 1: ESP Electrical Signature Analysis – ESPs that have no instrumentation and only electrical signature (current & voltage) capture is possible through the motor control cabinet.
- Model 2: ESP Electric, Pressure and Temperature Signature Analysis – ESPs which have the following data available through a pump controller:
- Downhole motor electrical signature data – voltage, current, frequency
- Motor Speed of RPM
- Tubing Pressure
- Casing Pressure
- Discharge Pressure
- Pressure Intake
- Motor Winding Temperature
- Overall Vibration of the Pump
During our comparison of both these installations we have identified that Model 2 performs marginally better than Model 1. The key challenge with model 2 is that it requires downhole sensors that fail very often or before the ESP fails. Data collected by us shows that downhole sensor failure is the most common issue encountered in ESP predictive maintenance. Model 1 though a little less accurate but is more cost effective and reliable.
Faults detected by such a ESP Predictive Maintenance system:
The following faults and issues can be identified with this data:
- Motor Faults
- Pump Faults
- Bearing and Coupling Issues
- Pump Efficiency issues
- Well or Reservoir Condition
- Gas Lock
- Gas Slugging
- Frac hit or lift problem
- Unit cycling in PID/GLR mode
- Erratic tubing pressure or tubing malfunction
- High Winding Temperature issue
- Speed issues and VFD issues
- Solid plugging
- Broken shaft
- High hole, leaks, increased inflow or recirculation
- Power or drive issue
The top five faults in an ESP as per data collected by us is:
- Donwhole sensor failure
- Gas Slugging
- Power and VFD issues
- Gas Locking
- Motor Failure
Downhole sensor failure usually does not impact production but leaves the ESP operator without insights into the operating conditions. This is also easy to detect with anomalies in the sensor data. We would leave this fault out of discussion as it does not impact production and reliability of the pump. A typical sensor failure looks like this:
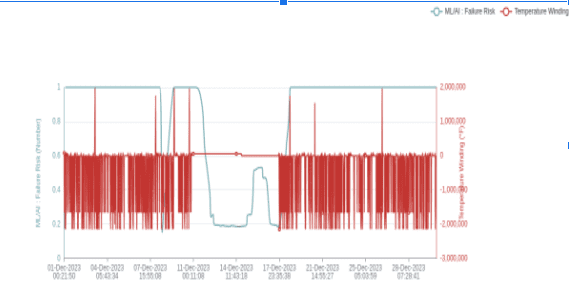
- Gas Slugging and Gas Locking: Accumulation and trapping of the free gas in the pump, which can reduce the effective liquid volume and the hydraulic force. A prolonged gas slug event can result into gas locking
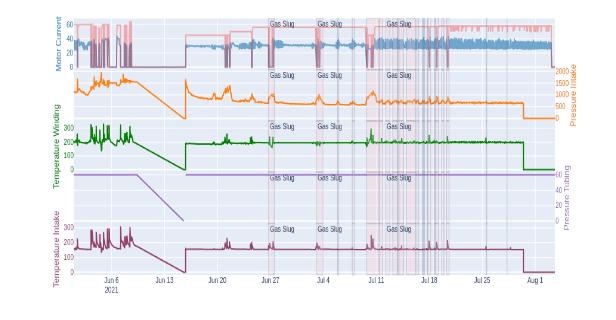
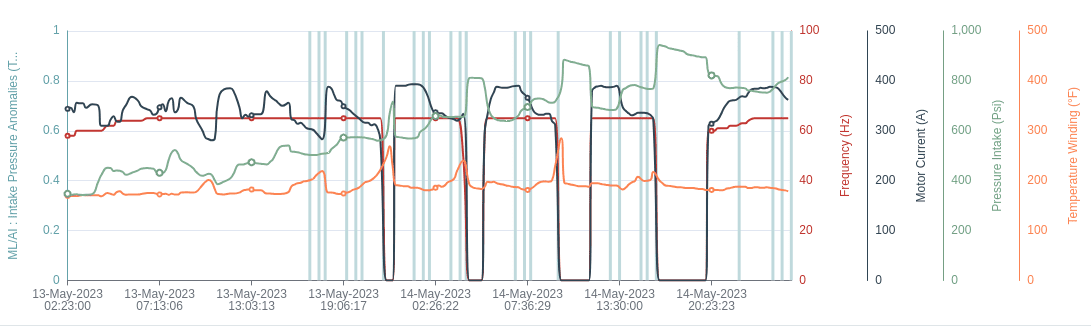
Motor Failure: Various motor failure conditions like air gap eccentricity, broken bar in rotor and short circuit fault in stator etc are captured by applying various analysis techniques like MCSA, EPVA, IPSA and Wavelet Analysis. These also help in detecting possible fault conditions in transmission system, VFD and various mechanical faults well in advance
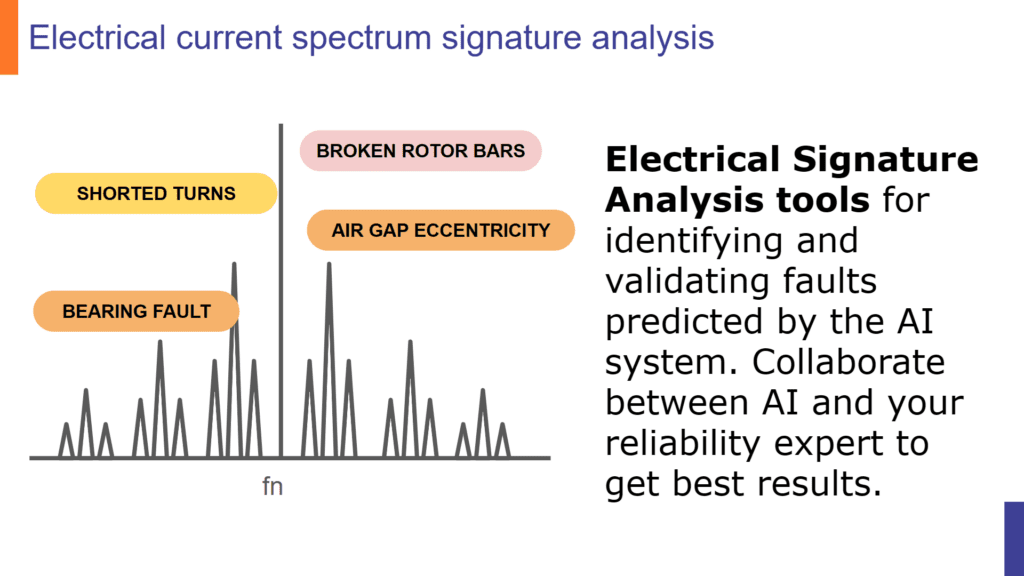
Our Approach:
We aimed to reduce delays in production by utilizing early warnings and insights to prolong the operational lifespan. Imagine being able to anticipate ESP failures days or even weeks beforehand. This foresight enables the mobilization of resources such as workover rigs and replacement parts, along with scheduling crews well in advance of any potential breakdown. In conventional oil field practices, this proactive approach can save significant time otherwise lost to deferred production. Simultaneously, access to dependable ESP operational insights empowers operators to fine-tune their operating parameters, effectively prolonging the lifespan of ESPs.
- Installation: Safely install the condition monitoring sensor inside the surface motor control cabinet to monitor the most important parts of the drivetrain at hard-to-reach places. This is a swift and hassle-free installation, compatible with both low- and medium-voltage machinery, including VFD-driven motors and other rotating equipment.
- Data capture:
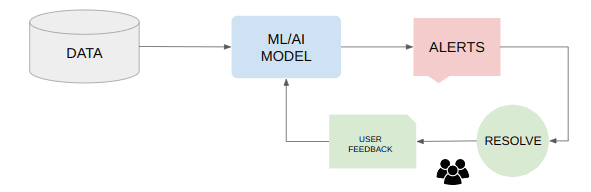
- Failure prediction: Proactively plan for various actions required through predictive alerts of upcoming failures. Leverage AI/ML models that accurately predicted upcoming asset failure on thousands of assets.
- Provide comprehensive and actionable alerts precisely when the customer requires them. Our comprehensive system coupled with trained AI models, will promptly notify about potential ESP failures and their underlying causes.
- Access to real-time ESP data to gain complete visibility both before and after downhole sensor failures occur. Empower the maintenance team with timely alerts regarding impending faults, including fault types and prioritized recommended actions based on urgency.
Our Solution: Case study of “A Large USA Oilfield Technology Solutions“
Story:
This success story is about a large Oilfield Technology Solutions company of USA. The company is a worldwide pioneer in the development of chemistry-based solutions, artificial lift systems, and highly engineered equipment and technologies. They assist clients in drilling for and extracting oil and gas safely, efficiently, and sustainably around the globe.
The company takes great pride in its reliability and efficiency as a major player in the oil and gas industry.
Insufficient Software for Pump Data Analysis challenged the company to properly maintain and safeguard their pumps. As a result, technicians had to routinely inspect each pump, requiring a significant amount of time and money for timely intervention.
The challenges in their daily operations, such as downtime, remote monitoring, and the need for real-time insights needed an immediate solution. The partnership with SenseGrow delivered them a prompt, innovative, and reliable solution. The primary focus of this collaboration was implementing a predictive maintenance (PdM) solution specially tailored for Electrical Submersible Pump (ESP) systems.
Faults Addressed:
Gas Slugging, Gas Locking, Frac Hits, HWT issues, Intake Pressure Anomalies; Anomaly Detection and Failure Risk Prediction for ESP
Progression:
In the Proof of Concept (POC) phase, over 250 pumps were assessed to showcase the accuracy of SenseGrow’s predictive maintenance ESP model. The customized solution not only identified potential faults but also demonstrated its ability to proactively address issues before they became major problems. With this approach, the model greatly improved uptime and operational reliability. The company decided to extend the implementation to 600 pumps first and then to 1251 pumps.
Outcome:
SenseGrow’s real-time condition monitoring expertise proved valuable for the company, a leader in oilfield production technology. With an extensive network of ESPs, they required a PdM solution capable of efficiently detecting and addressing anomalies while generating faults based on those detected. By integrating the customized PdM solution into their operations, the company was able to meet this critical need.
Challenges in Implementing Machine Learning:
While machine learning holds tremendous potential, its implementation comes with challenges. Issues such as quality as well as availability of continuous data, the interpretability of complex models, and end user feedback and co-operation must be addressed to ensure the successful integration of machine learning into existing ESP maintenance practices. Collaborative efforts within the industry, investments in research and development, and the establishment of best practices are recommended to ensure widespread adoption of these cutting-edge solutions.
Conclusion:
In conclusion, the collaboration of machine learning and ESP maintenance represents a paradigm shift in the oil and gas industry. The same applies to ESPs in water application. By embracing these advanced technologies, companies can significantly enhance the reliability of ESPs, optimize production efficiency, and ultimately achieve greater operational success. The time is ripe for the industry to adopt machine learning as a key enabler for predictive maintenance in electrical submersible pump systems.